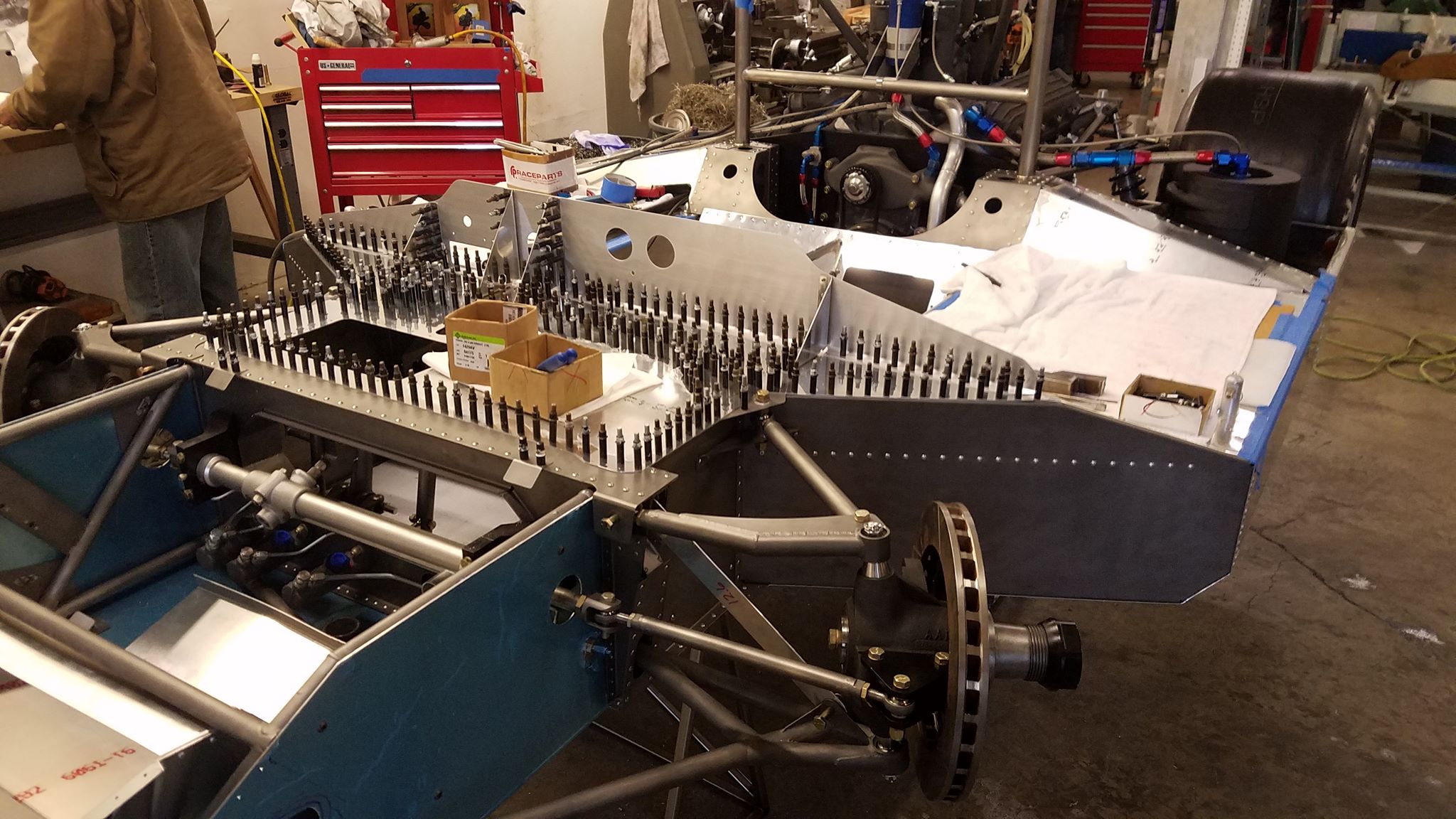
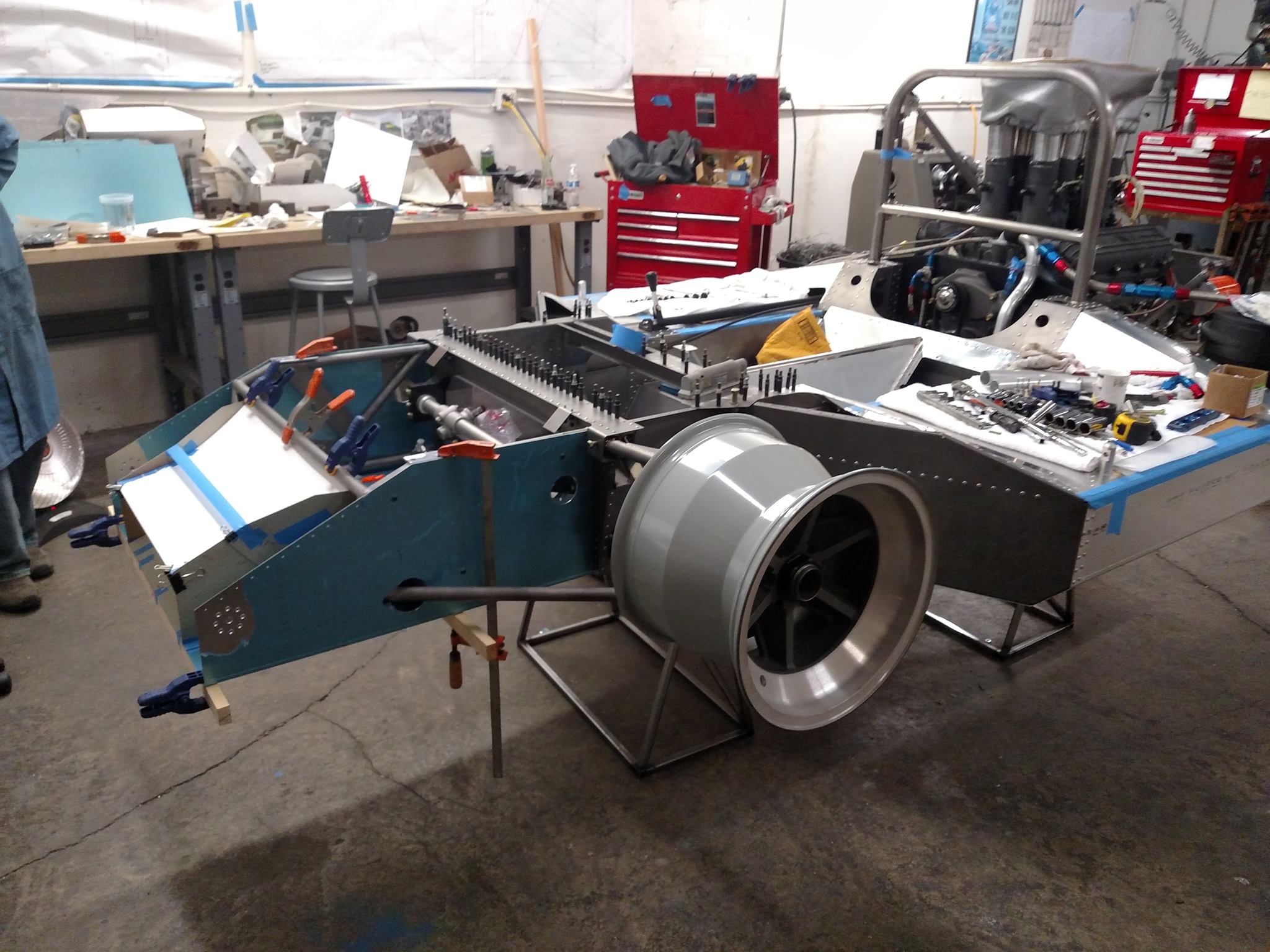
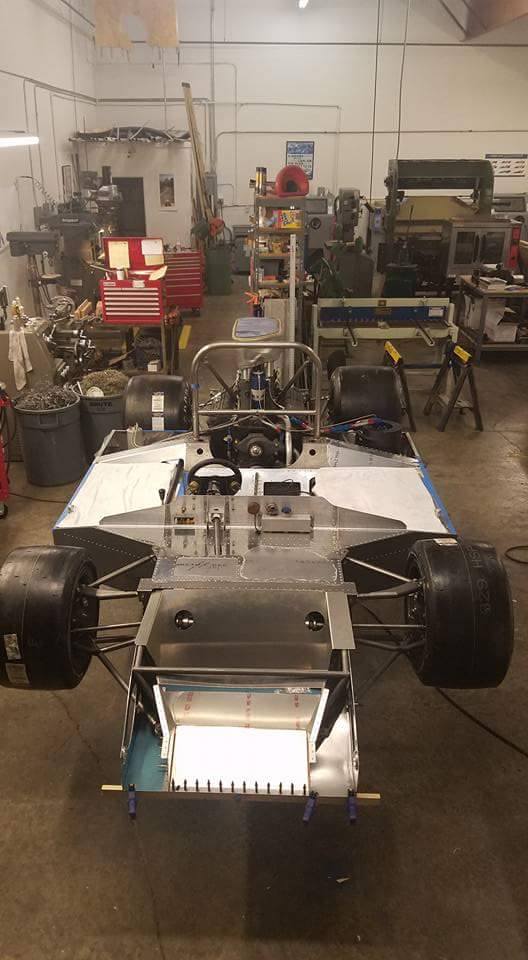
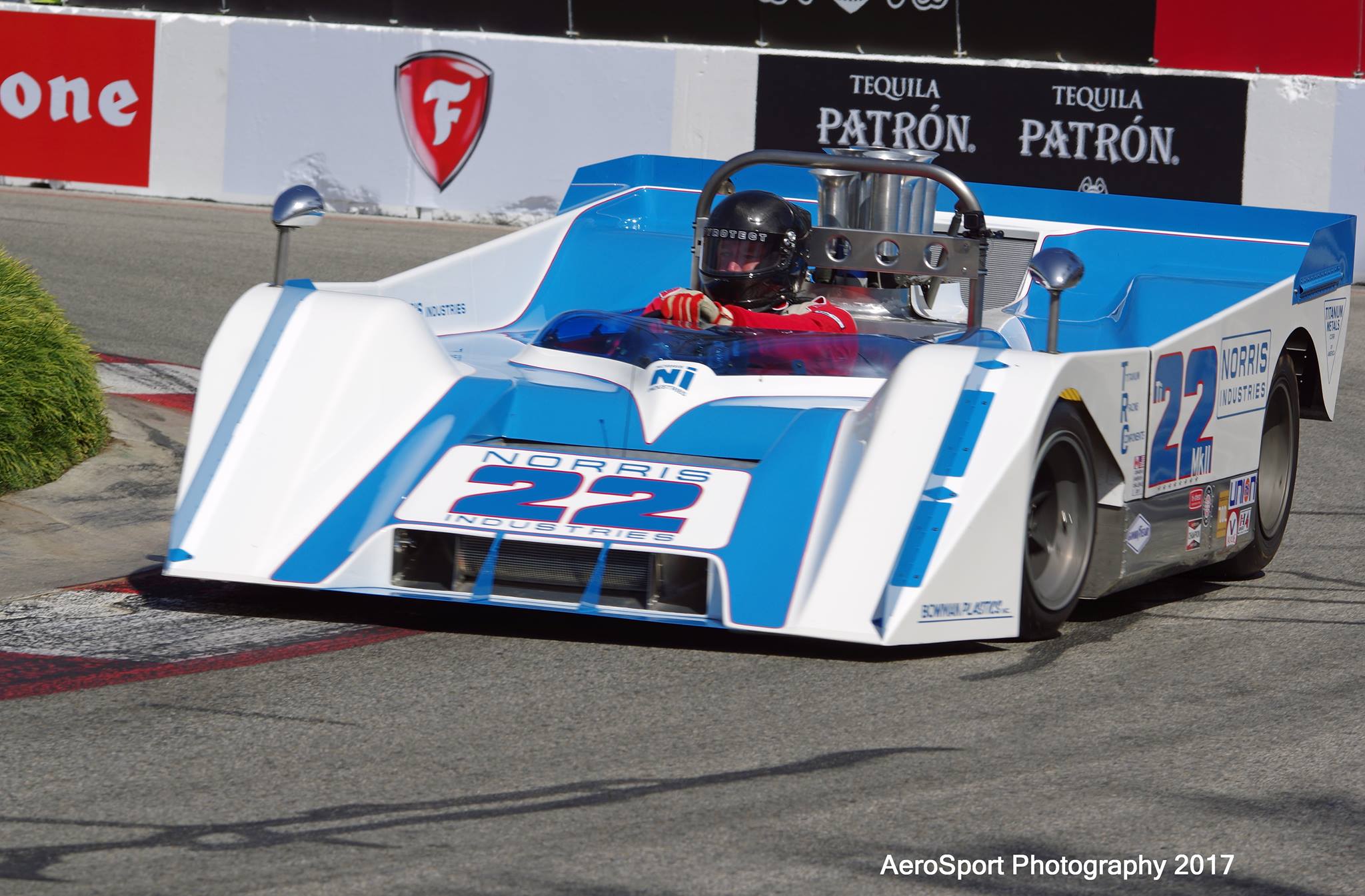
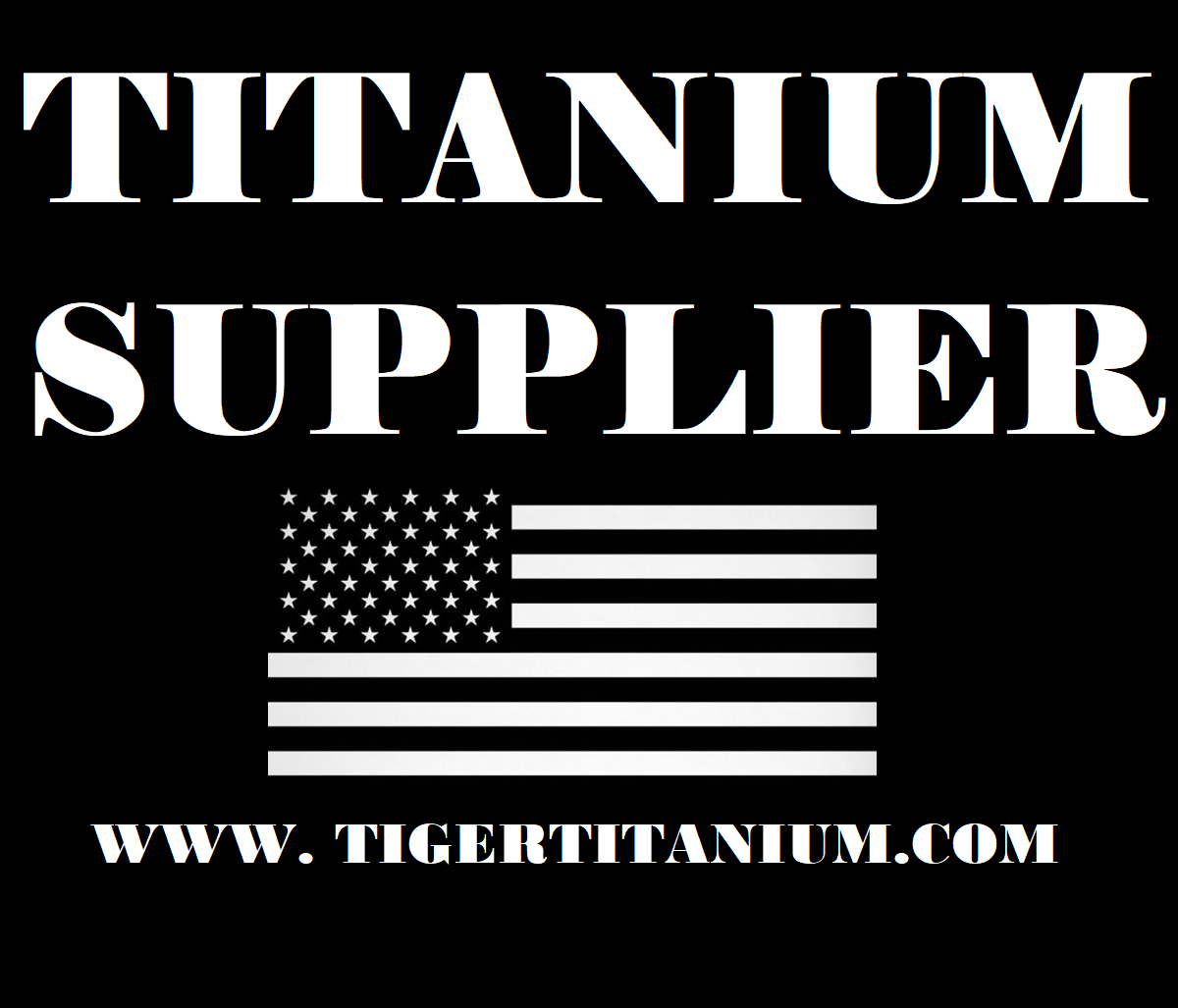
Articles about Titanium
Click for more. Fabian 2023-03-04
Click for more. Fabian 2023-03-04
Click for more. Fabian 2023-03-04
Click for more. Fabian 2023-03-02
Click for more. Fabian 2023-02-23
Click for more. Fabian 2023-02-22
Click for more. Fabian 2023-02-22
Click for more. Fabian 2023-02-22
Click for more. sean 2023-02-20
Click for more. 2017-12-21
Click for more. Charles Dohogne 2017-09-02
Click for more. Chuck Dohogne 2015-05-19
Click for more. Charles Dohogne 2015-02-22
Click for more. Charles Dohogne 2014-06-30
Everything about the automotive/transportation industry these days is based on economy. MPG is the watchword. Engines are built smaller and smaller and run at higher RPMs in the name of fuel economy. All moving parts have vibration harmonics, ranges where they try to rip themselves apart. A big old V-8, running at 3000 RPM requires only very basic balancing to run smoothly, while a four cylinder engine, at much higher speed, is little less than a fatigue test machine. Reducing the weight of the rapidly moving parts in the engine is the only way to reduce the inherent forces. Titanium connecting rods and piston pins weigh half as much as high quality, aftermarket steel parts. Reduced rotating and reciprocating mass means that balance weights in the crank shaft can also be reduced. Bearing life is extended and vibration generated heat is reduced also. Modern roller-tappet cams try to open and close the valves at very high acceleration rates. Since Force still equals mass times acceleration, reducing the mass is the only way to reduce the forces required to move the valves rapidly. Titanium valves, springs, retainers and lifters do a fine job. In addition, the lower mass of Titanium springs allow them to operate at much higher cyclic rates without harmonics and without the hysteresis (heat and noise, energy) losses of steel springs. In extreme drag race use, steel springs fail (relax) and must be replaced after one 5 second run (lots of work!!) Titanium springs last for 30 runs. Many other transportation uses for Titanium are apparent. Consider tanker trucks used for chemical transport. Road use rules limit the total weight of the truck plus load. A Titanium tank is vastly stronger, half the weight and much more corrosion resistant, allowing an over thirty percent increase in usable load. Two trucks with their associated drivers, taxes and fuel use on the road in place of three.
To understand and use Titanium, you must first forget most of what you know about metals. A metal's physical properties are controlled by its crystal structure. Titanium has a "hexagonal close packed" structure, other structural metals, Iron, Aluminum and Magnesium, are "Cubic." If you are a real student of structures, you know that the ideal hexagonal and cubic structures are the same, just viewed from a different perspective. Titanium’s hex is almost, but not quite, ideal. This is a very important feature that gives Titanium some of its outstanding properties.
Even the old, very common Titanium alloy 6-4 (6% Al, 4% V) has a higher strength to weight ratio than any steel or Aluminum alloy. Add in outstanding resistance to corrosion, fatigue and creep and Titanium really shines. Corrosion resistance is a good example of how odd-ball Titanium can be. Gold and Platinum are corrosion resistant because they are inert, Titanium is corrosion resistant because it is highly reactive.
Scratch a Titanium surface and it instantly reacts with air to reform the TiO2 surface. Add acid and electric current to drive the reaction and the TiO2 just gets thick enough to stop the reaction, called anodizing. Even stranger, it works both ways. Plating shops use Titanium for anode baskets to hold the metal to be dissolved and cathode racks to hold the pieces to be plated.
Toughness is another property of materials that shows the odd nature of Titanium. A notch in a metal bar concentrates the stress at that point. The testing standard is a notch with a radius of 0.010 inches, which yields a 6.5 X stress concentration at the root of the notch. A steel or Aluminum notched bar tensile test will fail at a stress much lower than a smooth test bar. Titanium gets stronger. A 6-4 bar, heat treated to 165KSI smooth will yield over 200KSI notched bar. The same concentration takes place, but the Titanium work-hardens under the notch instead of cracking. The hexagonal structure has less available slip planes, but, again, it is almost ideal, so it resists cracking.
Welcome to the wonderful world of TITANIUM!!
Discovered in 1791 by Reverend William Gregor, an English chemist and mineralogist. It was named after the Titans of Greek mythology by Martin Heinrich Klaproth, who also discovered Titanium in the same year.
Titanium is being used in a variety of fields including medicine, sports, marine and aerospace.
Titanium is known for its high strength to weight ratio. Titanium is as strong as steel but about 42% lighter. It is 60% heavier than aluminum, but two times as strong. Titanium also has a high level of corrosion resistance. Due to its light weight properties, titanium is used in retail products from eyeglasses to premium golf clubs and other sports equipment. Titanium is used for high quality jewelry such as watches and rings due to its hypoallergenic properties. For those who are sensitive or allergic to other metals such as gold, silver or nickel, titanium offers an alternative. Its silver color is similar to that of sterling silver, but titanium does not tarnish.
Titanium alloys are bio-compatible with the human body and thus are used for orthopedic implants, including artificial hips, dental implants, bone implants and pacemakers.
Titanium is used for aircraft, bicycles, knives, robots, jewelry and rockets where light weight and strength and the ability to tolerate extreme temperatures are necessary. Titanium has excellent resistance to sea water and is used in the marine industry and also for structures for ocean drilling and many parts that are exposed to salt water.
Titanium is used more and more every day for applications where light weight and high strength are required.
Structural metals are rated for their resistance to failure under stress (fracture toughness) by a factor called K1C. We start with a pre-cracked specimen and measure the stress needed to cause the crack to grow. In air test, Titanium and its alloys show very high K values when compared with other metals. When a corrosive environment (usually standard sea salt) is added to the test, we can rate metals with a factor called KISCC, for the onset of Stress Corrosion Cracking. The failure mode is quasi-cleavage, no ductile deformation on the crack surface. The inter-granular (along grain boundaries, not through grains) has a definitive "Rock Candy" appearance. All calculations are based on an infinite length crack, edge effects, ductility from the free surface, invalidates the test if over an arbitrary 10%.
Thin sheet specimens work well for other metals, but Titanium is so tough, thick plate is required for K1C and KISCC testing. Because of its outstanding resistance to corrosion, Titanium was thought to be immune from stress corrosion failure. Then in 1965 Brown, at the NRL, reported SCC in 6-4 Titanium! He had seen Rock Candy!!! Nothing in science is accepted until it is repeated by another independent lab. My boss called me in and appointed me as our "expert" on SCC of Titanium.
I found that SCC is defined as delayed cracking at a stress below the yield strength of the material. So long term testing of thick plate specimens was required. I built a huge rack with recording timers and other equipment. Because of the very high fatigue limit ( 70% for 6-4, 50% for steels) making the high cycle, low stress fatigue cracks in many one inch thick plate specimens was a chore! Normal production “in spec." materials showed nothing, so I had our melt lab produce "Off spec" ingots that were rolled down to the one inch thickness. Still nothing, so I tested unusual heat treatments. Finally, after six full months of work, I at last saw my rock candy surface!
I found that I must produce just the right starting fatigue crack in material that was over spec in both Aluminum and Oxygen content. I had to heat treat the material for long times at 1300F to precipitate the intermetallic compound Ti5Al3 in the microstructure. I had to start the salt water drip before applying any stress to avoid work hardening of the root of the crack. Then I did the math, no SCC. The root stress was well over the yield strength of the metal. I never saw true Stress Corrosion Cracking in 6-4 in sea water and I know of no one else finding it.
One interesting side note: we used full lab prep for our sea salt solutions. To see how important this was, we diluted the solution by 50%, then another 50%, then another with the same results. We tested pure distilled water, same results! We had always seen some variation in our baseline "air" testing that overlapped our sea salt tests. Humid days gave lower tests. Just the ad/absorbed film of water in the crack from the air can skew the test results. Aint Science wonderful????